Joints & Sensors
What if the secret to perfect humanoid robot motion isn't just about advanced sensors or cutting-edge algorithms? What if it's all about how we design the joints?
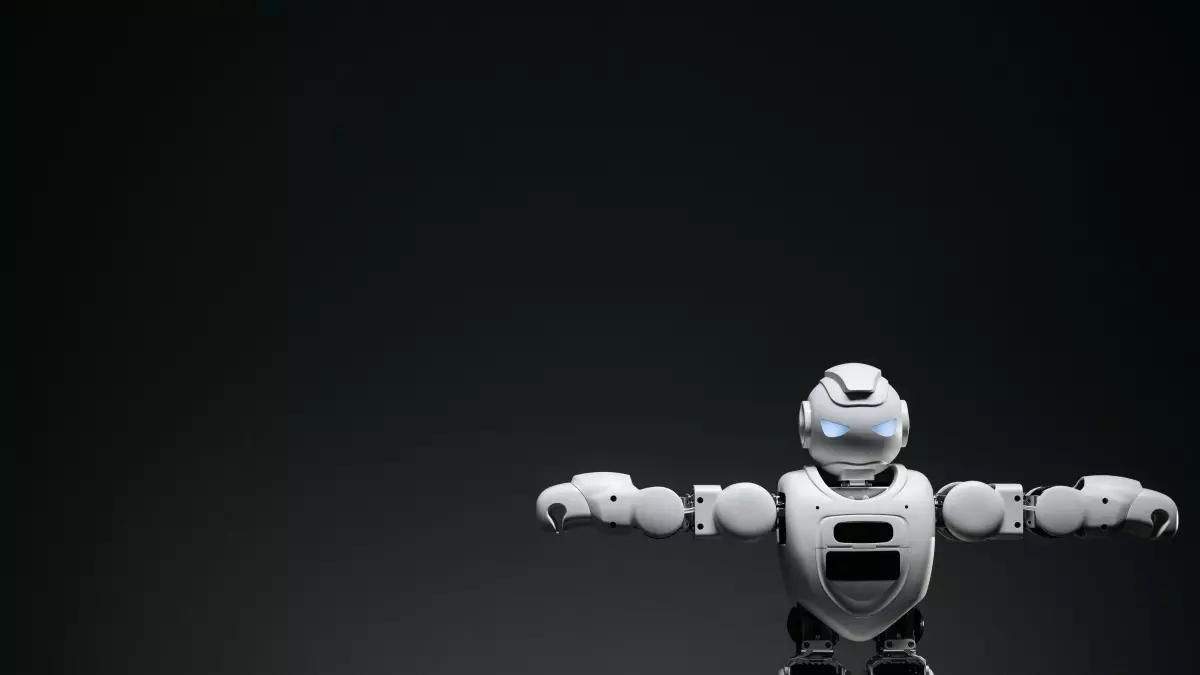
By Sarah Kim
Imagine a future where humanoid robots move with such fluidity and grace that you can't tell the difference between them and a human. They walk, run, and even dance with a level of precision that would make professional athletes jealous. But here's the kicker: it's not just the sensors or the AI that makes this possible. It's the way their joints are designed. Yep, the very same joints that we often overlook in favor of flashy sensors and complex algorithms.
Now, let's snap back to reality. While we're not quite there yet, humanoid robots are already making huge strides in realistic motion. And it's not just because of their sensors. Sure, sensors are important, but the design of the joints plays a massive role in how these robots move. In fact, the way joints are designed can either enhance or limit the effectiveness of the sensors. So, the big question is: which one matters more—joint design or sensor placement?
The Role of Joint Design
Let's start with the joints. In the world of humanoid robots, joints are like the hinges of a door. They determine how much freedom of movement a robot has and how smoothly it can transition between different motions. A well-designed joint allows for a wide range of motion, which is crucial for tasks like walking, running, or even picking up objects.
But here's the thing: not all joints are created equal. Some joints are designed to mimic the human body's natural movements, while others are more rigid and mechanical. The more human-like the joint, the more fluid the robot's movements will be. This is why joint design is such a critical aspect of humanoid robot development. The more realistic the joint, the more natural the robot's movements will appear.
Take the knee joint, for example. In humans, the knee is a complex joint that allows for both bending and slight rotation. In humanoid robots, replicating this movement is no easy task. It requires a combination of mechanical engineering and advanced materials to create a joint that can bend and rotate in a way that mimics the human knee. If the joint is too stiff, the robot's movements will look robotic (pun intended). But if the joint is too loose, the robot will lack stability.
Sensor Placement: The Unsung Hero
Now, let's talk about sensors. While joint design is crucial for movement, sensors are what give humanoid robots the ability to perceive their environment and adjust their movements accordingly. Sensors are like the robot's eyes and ears, allowing it to detect obstacles, measure distances, and even sense pressure.
But here's the catch: the effectiveness of these sensors depends largely on where they're placed. If a sensor is placed too far from a joint, it might not be able to accurately measure the joint's position or movement. On the other hand, if a sensor is placed too close to a joint, it might get overwhelmed by the constant movement and fail to provide accurate data.
For example, placing a sensor near the robot's elbow joint can help the robot determine how much force it needs to apply when picking up an object. But if that sensor is too far from the elbow, it might not be able to accurately measure the force needed, leading to clumsy or imprecise movements.
Finding the Balance
So, which one is more important: joint design or sensor placement? The truth is, it's not an either-or situation. Both joint design and sensor placement play a crucial role in achieving realistic humanoid robot motion. In fact, they complement each other.
A well-designed joint can enhance the effectiveness of a sensor, and vice versa. For example, a flexible joint allows for a wider range of motion, which means the sensor has more data to work with. On the flip side, a well-placed sensor can provide real-time feedback to the joint, allowing the robot to adjust its movements on the fly.
In many ways, it's like the relationship between a car's engine and its tires. The engine provides the power, but it's the tires that determine how that power is applied to the road. Similarly, joint design provides the range of motion, but it's the sensors that determine how that motion is applied in real-world situations.
The Future of Humanoid Robot Motion
As humanoid robots continue to evolve, the relationship between joint design and sensor placement will become even more important. In the future, we might see robots with joints that are even more flexible and human-like, allowing for a wider range of motion. At the same time, sensors will become more advanced, providing even more accurate data about the robot's environment.
One exciting possibility is the development of "smart joints" that combine joint design and sensor technology into a single, integrated system. These smart joints would not only provide a wide range of motion but also collect real-time data about the joint's position, speed, and force. This data could then be used to adjust the robot's movements in real-time, allowing for even more fluid and realistic motion.
Another possibility is the use of AI to optimize the relationship between joint design and sensor placement. By analyzing data from the robot's sensors, AI algorithms could determine the optimal joint design for a given task, allowing for more efficient and precise movements.
What Happens Next?
So, what's next for humanoid robots? As technology continues to advance, we can expect to see even more realistic and fluid movements from these robots. The key will be finding the perfect balance between joint design and sensor placement. By optimizing both, we can create robots that move with the grace and precision of a human.
But here's the real question: will we ever reach a point where humanoid robots move so naturally that we can't tell the difference between them and a human? Only time will tell, but one thing's for sure—it's going to be an exciting journey.