End Effectors
Back in the early days of robotics, robots were mostly limited to repetitive tasks like lifting or moving objects. But as industries grew more complex, so did the demands on robots. Enter the end effector—the unsung hero of modern robotics. It’s the part of the robot that interacts with the environment, and without it, robots would be nothing more than glorified mechanical arms.
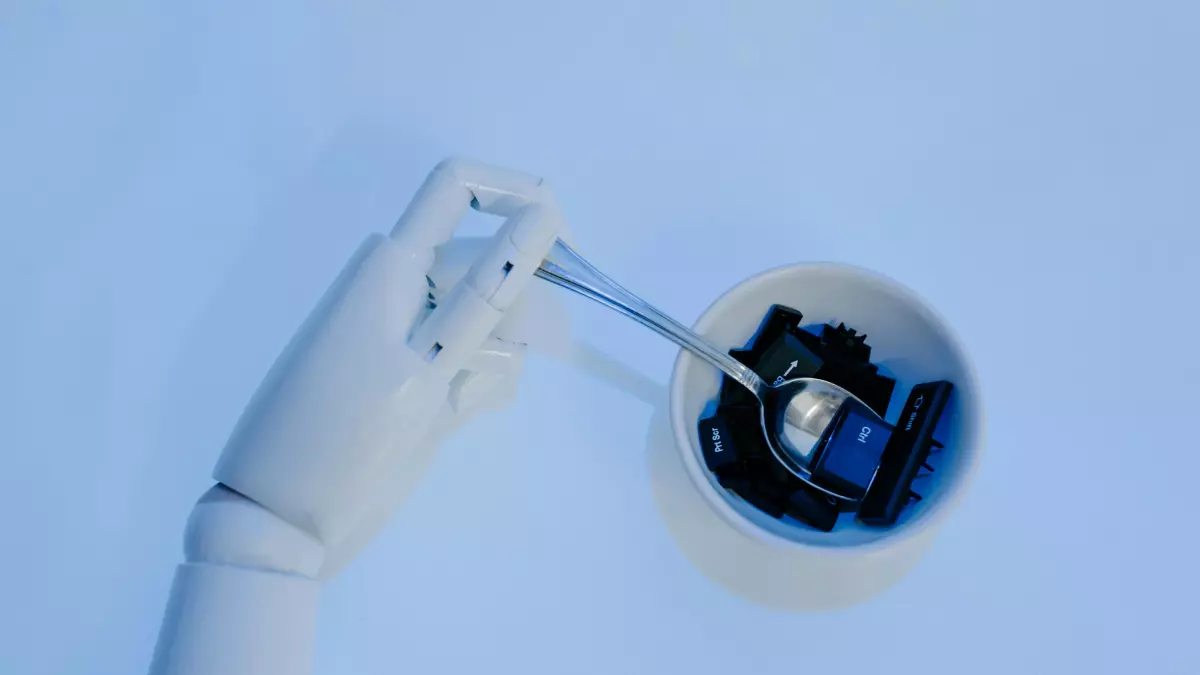
By Carlos Martinez
End effectors are the business end of a robot. They’re the tools that allow robots to perform tasks like gripping, welding, cutting, or even performing surgery. If you think about it, they’re like the hands of a robot, and just like human hands, they need to be versatile, precise, and reliable. But how exactly do these robotic 'hands' work, and what makes them so crucial to the future of automation?
Let’s start with the basics. An end effector is the device at the end of a robotic arm, designed to interact with the environment. It can be a gripper, a tool, or a sensor, depending on the task. The design of an end effector depends on the application. For example, a robot in a factory might have a simple gripper to pick up and move parts, while a surgical robot might have a highly specialized tool for performing delicate procedures.
But here’s where it gets interesting: the technology behind end effectors has evolved dramatically over the past few years. We’re no longer talking about simple mechanical claws. Modern end effectors are equipped with sensors, actuators, and even AI-driven software that allows them to adapt to different tasks and environments. This is what makes them so powerful in industries like manufacturing, healthcare, and even space exploration.
Types of End Effectors
There are several types of end effectors, each designed for specific tasks. The most common types include:
- Grippers: These are the most basic type of end effector and are used to pick up and hold objects. They can be mechanical, pneumatic, or even magnetic, depending on the application.
- Welding Guns: Used in manufacturing, these end effectors are designed to perform welding tasks with high precision.
- Cutting Tools: These are used for tasks like cutting, drilling, or milling. They need to be extremely precise, especially in industries like aerospace or automotive manufacturing.
- Force/Torque Sensors: These sensors allow the robot to measure the force or torque being applied to an object, which is crucial for tasks that require delicate handling, like assembling electronics or performing surgery.
- Vacuum Cups: Often used in packaging or material handling, vacuum cups can pick up objects with smooth surfaces by creating a vacuum seal.
Each of these end effectors has its own set of challenges and advantages. For example, grippers need to be strong enough to hold objects securely but gentle enough not to damage them. Welding guns need to be precise and fast, while cutting tools need to be durable and sharp. And sensors? Well, they need to be accurate and responsive, especially in delicate tasks like surgery or electronics assembly.
The Role of AI and Machine Learning
One of the most exciting developments in end effector technology is the integration of AI and machine learning. In the past, end effectors were limited by their programming. They could only perform the tasks they were explicitly designed for. But with AI, end effectors can now learn from their environment and adapt to new tasks on the fly.
For example, a robot equipped with an AI-driven end effector could learn how to pick up objects of different shapes and sizes without needing to be reprogrammed. It could also adjust its grip based on the material of the object, ensuring that it doesn’t damage delicate items. This kind of adaptability is crucial in industries like e-commerce, where robots need to handle a wide variety of products quickly and efficiently.
Machine learning also plays a role in improving the precision of end effectors. By analyzing data from previous tasks, an AI-driven end effector can fine-tune its movements to be more accurate and efficient. This is especially important in industries like healthcare, where even the smallest mistake can have serious consequences.
Challenges and Future Developments
Despite all the advancements in end effector technology, there are still some challenges that need to be addressed. One of the biggest challenges is durability. End effectors are often exposed to harsh environments, and they need to be able to withstand wear and tear without losing their precision.
Another challenge is cost. High-tech end effectors, especially those equipped with AI and sensors, can be expensive to produce and maintain. This can be a barrier for smaller companies that want to adopt robotic automation but can’t afford the upfront costs.
But the future looks bright. Researchers are working on developing new materials and designs that will make end effectors more durable and cost-effective. There’s also a lot of work being done on improving the integration of AI and machine learning, which will make end effectors even more adaptable and efficient.
In the end, end effectors are a crucial part of the robotics ecosystem. They’re the tools that allow robots to interact with the world, and without them, robots would be pretty useless. As technology continues to evolve, we can expect to see even more advanced end effectors that will push the boundaries of what robots can do.