Servo Systems
What do a ballet dancer and a robot arm have in common? Both rely on precise, controlled movements to perform their tasks flawlessly. But while the dancer uses years of training, the robot arm depends on something far more technical: servo systems.
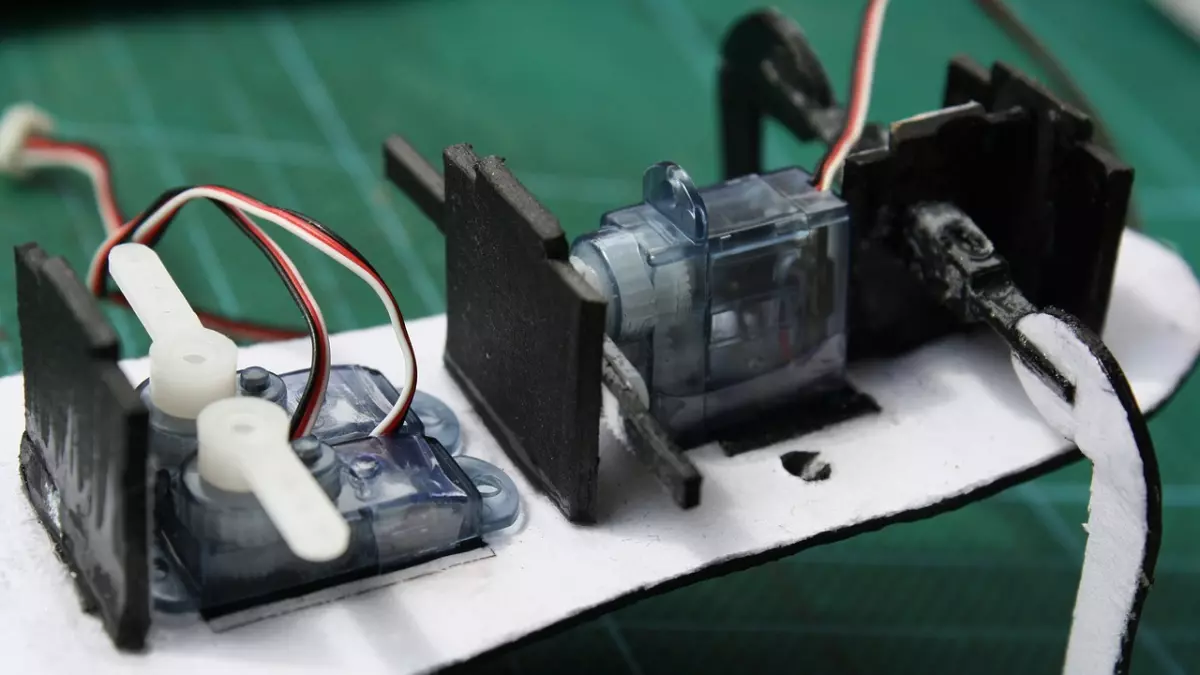
By Sophia Rossi
Servo systems are the unsung heroes of robotics, quietly working behind the scenes to ensure robots move with the precision and accuracy we’ve come to expect. Whether it's a robotic arm assembling parts in a factory or a humanoid robot performing delicate tasks, servo systems are the key to making it all happen. But what exactly are these systems, and how do they work? Let’s dive into the world of servo systems and explore how they enable robots to perform complex, precise movements.
What is a Servo System?
A servo system is a closed-loop control system that uses feedback to achieve precise control of angular or linear position, velocity, and acceleration. In simpler terms, it’s the system that allows a robot to move its parts with pinpoint accuracy. The term 'servo' comes from the Latin word 'servus,' meaning servant, and that's exactly what these systems do—they serve the robot by controlling its movements.
At the heart of a servo system is the servo motor, which is responsible for executing the movement. But the motor doesn’t act alone. It’s part of a larger system that includes a sensor to provide feedback on the motor’s position, a controller to process that feedback, and a driver to regulate the power supplied to the motor. Together, these components form a loop that constantly adjusts the motor’s position to ensure it matches the desired outcome.
How Servo Systems Work
Let’s break it down step by step:
- Command Input: The system receives a command, such as 'move the arm to this position.'
- Feedback: A sensor (often an encoder) measures the current position of the motor and sends this information back to the controller.
- Comparison: The controller compares the current position with the desired position. If there’s a difference, it calculates the necessary adjustments.
- Correction: The driver adjusts the power supplied to the motor to correct the position, ensuring the robot moves to the desired location.
- Repeat: This process repeats continuously, allowing for real-time adjustments and smooth, precise movements.
This closed-loop system is what allows robots to perform tasks that require high levels of precision, such as assembling tiny components or performing surgery.
Hardware Components of Servo Systems
Now that we understand how servo systems work, let’s take a closer look at the hardware that makes it all possible.
- Servo Motor: The star of the show, the servo motor is responsible for generating the movement. There are different types of servo motors, including DC servos, AC servos, and stepper motors, each with its own advantages and use cases.
- Encoder: This sensor provides feedback on the motor’s position. Encoders can be incremental or absolute, with absolute encoders providing more precise position data.
- Controller: The brain of the system, the controller processes the feedback from the encoder and determines the necessary adjustments to the motor’s position.
- Driver: The driver regulates the power supplied to the motor, ensuring it receives the correct amount of voltage and current to achieve the desired movement.
These components work together to create a system that can achieve incredibly precise movements, even in complex environments.
Software Behind Servo Systems
While the hardware is essential, the software is what brings the system to life. Servo systems rely on sophisticated algorithms to process feedback and make real-time adjustments to the motor’s position. These algorithms are often based on PID control (Proportional-Integral-Derivative), a control loop mechanism that continuously calculates the error between the desired and actual position and adjusts the motor’s output accordingly.
In addition to PID control, modern servo systems may also incorporate machine learning and AI algorithms to improve performance over time. For example, a robot equipped with AI could learn to optimize its movements based on past performance, reducing errors and improving efficiency.
Applications of Servo Systems in Robotics
Servo systems are used in a wide range of robotic applications, from industrial automation to medical robotics. Here are a few examples:
- Industrial Robots: Servo systems enable industrial robots to perform tasks like welding, painting, and assembly with high precision and repeatability.
- Medical Robots: In the medical field, servo systems are used in surgical robots to perform delicate procedures with extreme accuracy.
- Humanoid Robots: Servo systems allow humanoid robots to mimic human movements, enabling them to walk, grasp objects, and interact with their environment.
- Autonomous Vehicles: Servo systems are also used in autonomous vehicles to control steering, acceleration, and braking with precision.
The Future of Servo Systems
As robotics continues to evolve, so too will servo systems. We can expect to see even more advanced algorithms that enable robots to perform tasks with greater precision and efficiency. Additionally, the integration of AI and machine learning will allow servo systems to become more adaptive, learning from their environment and improving their performance over time.
In the future, we may also see the development of miniaturized servo systems that can be used in smaller, more compact robots, opening up new possibilities for applications in fields like nanotechnology and wearable robotics.
So, the next time you see a robot performing a complex task with flawless precision, remember that it’s not just the robot’s hardware or software that makes it possible—it’s the servo system working quietly behind the scenes, ensuring every movement is just right.