Robot Manipulation
Imagine a robot's arm as a master pianist—each finger moving with precision, grace, and purpose. But instead of playing Beethoven, it's assembling cars, performing surgeries, or flipping burgers.
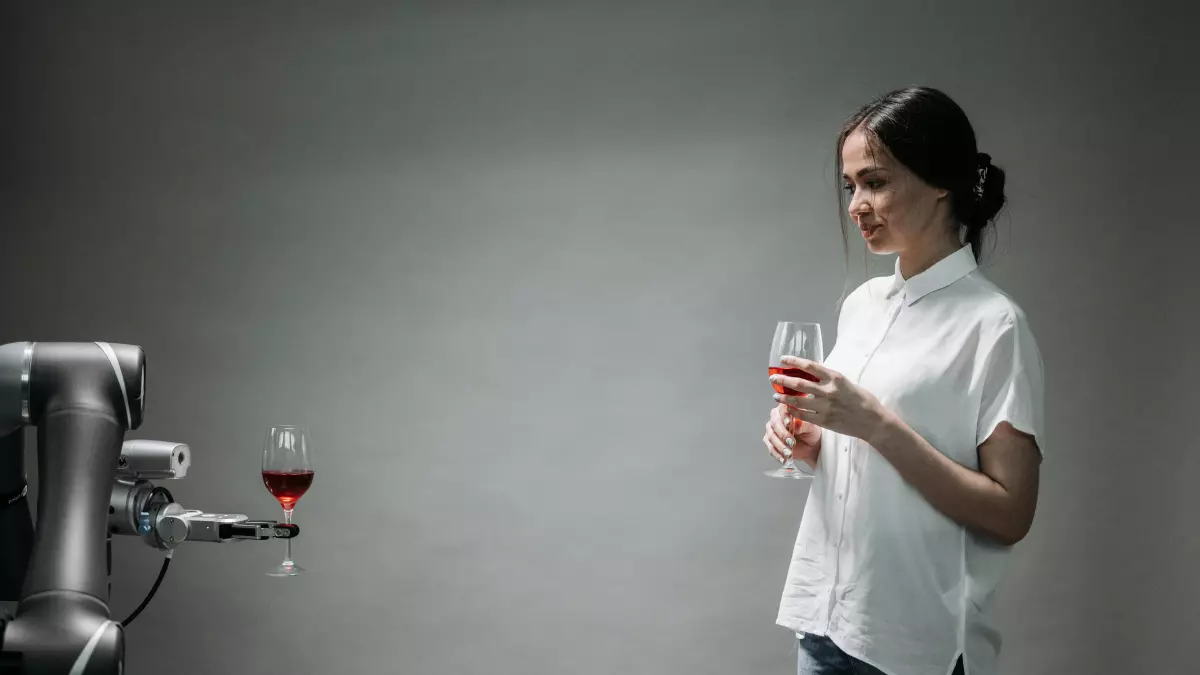
By Alex Rivera
Robot manipulation refers to the ability of a robot to interact with objects in its environment. In simpler terms, it's how robots use their 'hands' or manipulators to grasp, move, and manipulate objects. This is a critical aspect of robotics, especially in industries where precision and dexterity are key. From assembling tiny components in electronics to handling delicate surgical instruments, robot manipulation is the backbone of many modern automated systems.
But how do these robots achieve such precision? What makes them capable of handling objects with such care or force, depending on the task? The answer lies in the combination of hardware design, control systems, and sophisticated software algorithms that work in harmony to create these mechanical marvels.
Hardware: The Skeleton of Manipulation
At the core of any robot manipulation system is the hardware—the physical components that make up the robot's 'body.' This includes the actuators, joints, and end-effectors (the 'hands' of the robot). The design of these components is crucial because it determines the robot's range of motion, strength, and dexterity.
For example, a robot arm designed for heavy lifting in a factory will have different hardware requirements than a robot used in delicate surgical procedures. The actuators (which are essentially the muscles of the robot) need to be powerful enough to perform the required tasks but also precise enough to avoid damaging the objects they're manipulating.
End-effectors come in many forms, from simple grippers to more complex multi-fingered hands that mimic human dexterity. The choice of end-effector depends on the task at hand—pun intended. A robot assembling electronics might need a fine-tuned gripper, while a robot in a warehouse might use a more robust claw to handle heavy packages.
Control Systems: The Brain Behind the Brawn
While hardware gives the robot its physical capabilities, control systems are what make it all work together. These systems are responsible for coordinating the movements of the robot's actuators and joints to achieve the desired manipulation tasks.
Control systems in robotics can be divided into two main types: open-loop and closed-loop systems. Open-loop systems operate without feedback, meaning the robot performs a pre-programmed sequence of actions without adjusting based on real-time data. Closed-loop systems, on the other hand, use feedback from sensors to adjust the robot's movements in real-time, allowing for more precise and adaptive manipulation.
For example, a closed-loop system might use force sensors to ensure that a robot doesn't apply too much pressure when handling a fragile object. This kind of feedback loop is essential for tasks that require a high degree of precision, such as assembling tiny components or performing surgery.
Software: The Algorithms Driving Precision
Now, let's talk about the software—the algorithms that drive the robot's manipulation capabilities. These algorithms are responsible for planning and controlling the robot's movements, ensuring that it can perform tasks efficiently and accurately.
One of the most important algorithms in robot manipulation is inverse kinematics. This algorithm calculates the joint angles needed for the robot's end-effector to reach a specific position in space. Essentially, it tells the robot how to move its 'arm' to get its 'hand' where it needs to be.
Another key algorithm is motion planning, which determines the path the robot should take to avoid obstacles and reach its target. This is especially important in dynamic environments where the robot needs to navigate around moving objects or people.
Finally, force control algorithms allow robots to adjust the amount of force they apply when manipulating objects. This is crucial for tasks that require a delicate touch, such as handling fragile items or performing intricate assembly tasks.
The Future of Robot Manipulation
As robots become more advanced, the future of robot manipulation looks incredibly promising. Advances in artificial intelligence and machine learning are enabling robots to learn from their experiences, improving their manipulation capabilities over time. This means that robots will not only be able to perform more complex tasks but also adapt to new environments and challenges.
One exciting area of research is the development of soft robotics, which uses flexible materials to create robots that can manipulate objects in ways that traditional rigid robots cannot. These soft robots could be used in a variety of applications, from healthcare to agriculture, where delicate handling is required.
Another area of development is human-robot collaboration, where robots work alongside humans to perform tasks. In these scenarios, robots need to be able to manipulate objects safely and efficiently while interacting with their human counterparts. This requires advanced control systems and algorithms that can adapt to the unpredictable nature of human behavior.
So, what's next for you? If you're a robotics enthusiast or professional, it's time to dive deeper into the world of robot manipulation. Whether you're designing the next generation of robotic arms or developing algorithms that drive precision, the future of robotics is in your hands—literally.